加固型8軸線運動控制器板卡
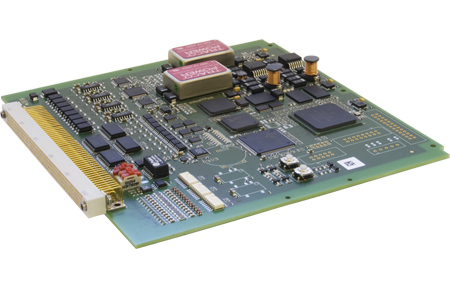
Motion Controller 8-Axis
For a leading Chinese OEM company SYS TEC electronic developed a ruggedized motion controller solution. The controller is C/C++ programmable and allows for synchronous operation of up to 8 axes within a 50μs cycle time. It was especially designed and optimized for use in embedded motion control applications that operate under harsh environmental conditions, such as often present in off-road mobile machinery.
The design is based on the ECUcore-5484. However, in order to ensure reliable operation under the specified parameters, the ECUcore-5484 was designed onto the application board. A performance-optimized multi-CPU design approach was chosen to achieve a 50μs synchronization cycle. This consist of the 32-bit ECUcore-5484 based Supervisory CPU circuitry, a digital signal processor (DSP) for control loop calculations and two FPGA for handling the I/O processing. All CPU’s are connected by a bus system. The Supervisory CPU runs an eCos real-time operating system with the user-application. It allows the user to access all device resources and therefore to keep full control over the systems behavior and its real-time characteristics. SYS TEC electronic developed the target platform board support package, the communication and I/O drivers and the control loop software running on the Supervisory CPU, the DSP and the two FPGAs. This software solution provides an API to the user application for configuring and executing moves, communicate via all provided interfaces and access the I/Os on the FPGAs.
The DSP, a TI TMS320C672x derivate, executes the hard real-time functions of the control loop, including the trajectory generation and interpolation. The control loop software supports position control and velocity control. Two FPGAs handle the I/O access. Within the FPGA firmware, eight A/B encoder input channels with an input frequency of up to 6MHz are available. The FPGA firmware also includes drivers for various absolute and incremental encoders, such as Encoders from Tamagawa, Positral Fraba and Netzer. In addition the controller features 8x pulse output channels with up to 2Mhz output frequency, 8x 24-bit ADC, 8x 24-bit DAC, 16x digital outputs and 24x digital inputs. The FPGA ensure that all I/O and encoder lines operate synchronously at a cycle time of 50μs. SYS TEC electronic implemented various hardware and software measures in order to protect the design, such as encrypted storage of FPGA firmware and the application firmware. The controller’s on-board communication interfaces comprise three RS232, a RS422, a 10/100Mbps Fast Ethernet and two CAN ports. All signals and power lines are available on a 128pin class-A industrial-grade board-to-board connector. This allows for plugging the board onto an applicable backplane, and therefore to enable setup of redundant system architectures. The Motion Controller Card was designed in two versions, whereof one version supports up to eight axis and the other version supports up to 4 axis.
During the development process the device has gone through extensive climatic, mechanical and EMC tests. After development and verification of the controller prototypes, the two controller versions were produced in serial at SYS TEC electronic.
SYS TEC electronic GmbH is a skills-based system house offering expertise in leading-edge embedded control technology. The company is based in Greiz/Germany and specializes in research, development and production of custom-tailored solutions and system components for applications in machine control, transportation and automation. SYS TEC electronic GmbH was founded in 1990 with its headquarters in Greiz. Since 2007 SYS TEC electronic operates an own production line in Reichenbach/Germany. In 2005 SYS TEC electronic GmbH established an office in Beijing/China to provide direct support and a native-speaking interface for customers in Mainland China and beyond.
|